L’injection thermoplastique est couramment utilisée pour produire des pièces identiques à une cadence importante. Elle est développée notamment pour les matières plastiques et élastomères.
L’excellence du détail comme les finitions de surface sont rendues possibles et idéales grâce à l’usinage de moules précis avec hautes pressions d’injection. On peut alors partir sur une production de masse ou à moyenne échelle.
Les fondamentaux
Il convient d’abord de faire un tour d’horizon de ce que sont le moulage par injection, les étapes de fabrication ainsi que les matières à utiliser.
Kesako ?
Le moulage par injection est une technique de fabrication à grande échelle de pièces en matières plastiques ou élastomères.
Ces composants sont ensuite utilisés dans de nombreux domaines : automobile, sport, électrotechnique, électroménager, mobilier, informatique. Concernant les pièces plastiques, leurs dimensions sont extrêmement variables, allant de quelques millimètres à plusieurs mètres.
L’injection est un processus où l’on fait fondre des granulés de plastique (toute catégorie choisie). Une fois fluidifiés, ils sont injectés sous pression pour remplir l’empreinte d’un moule avant de se solidifier en refroidissant pour obtenir le produit final.
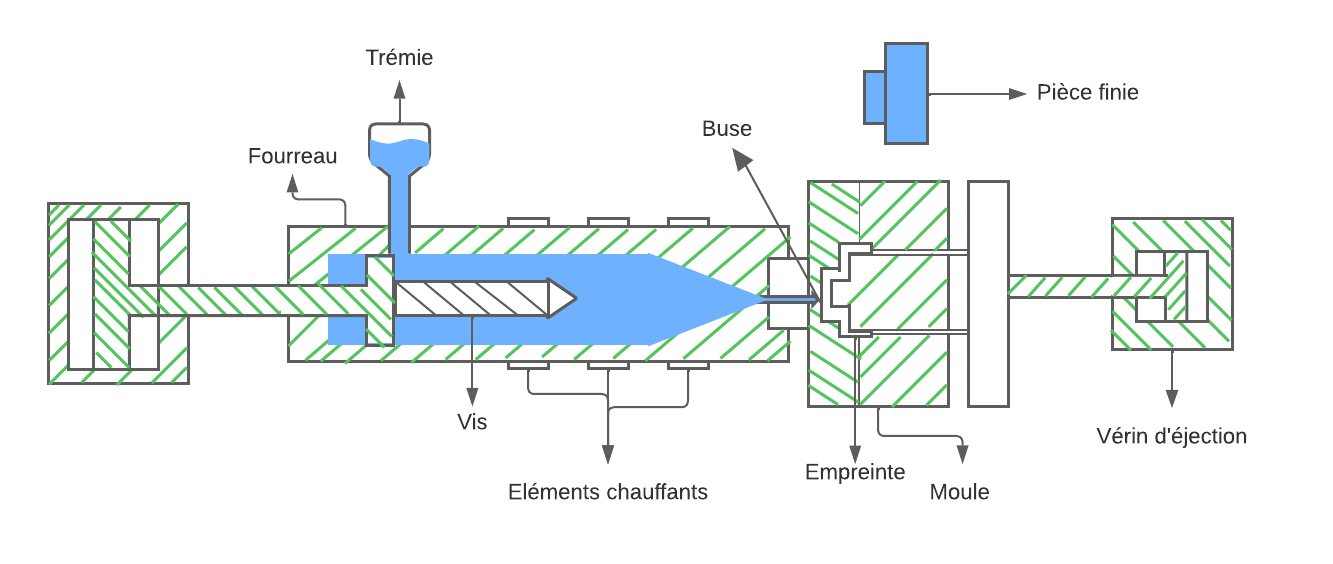
Les procédés de fabrication
L’injection thermoplastique consiste à ramollir la matière plastique et à l’injecter dans un moule froid sous forte pression. Le froid des parois du moule va solidifier la matière dans la forme (l’empreinte du moule) qui pourra alors être démoulée.
Voici les grandes étapes, le schéma est généralement le même :
- descente des granules dans la trémie
- ramollissement et dosage
- Injection sous pression
- refroidissement et éjection de la pièce fini
Les machines nécessaires
La presse à injecter à deux parties : le groupe d’injection/plastification et le groupe de fermeture. Ces groupes servent à la fusion et au transfert de la matière fondue dans le moule. Dans un cycle d’injection classique, les fonctions d’une presse sont :
- Alimenter en granulés
- Doser le volume de matière fondue
- Ouvrir/Fermer le moule puis verrouiller
- Injecter sous pression la matière fondue dans le moule
- Maintenir la matière sous pression
- Éjecter les pièces refroidies
Le moule d’injection est usiné en acier, de manière générale, afin de garantir sa longévité et d’augmenter la productivité. La dureté de l’acier et les équipements du moule sont définis en fonction des quantités de pièces à produire, des cadences souhaitées et de la matière à transformer. Ses fonctions sont :
- d’acheminer la matière jusqu’à l’empreinte/la cavité
- de mettre en forme la pièce à injecter
- de la refroidir : une bonne homogénéité thermique du moule assure les qualités esthétique et dimensionnelle de la pièce finie
- d’éjecter la pièce après refroidissement
Quelles matières plastiques ?
Pour le choix du matériau, cela dépend de vous, de vos besoins. Le matériau répond à des contraintes et des déformations auxquelles il devra résister. Le matériau idéal pour un usage spécifique est déterminé par plusieurs paramètres. Entre coût, contraintes fonctionnelles/esthétiques, résistance et résilience, il faut trouver un équilibre.
Les thermoplastiques sont couramment utilisés. Ils peuvent subir de nombreux cycles de fusion et de durcissement sans perte de leurs propriétés mécaniques. Ils se présentent sous forme de granulés ou de feuilles que l’on chauffe et met en forme par divers procédés. Comme il n’y a pas de liaisons chimiques, le recyclage/la fusion et la réutilisation sont possibles.
Chaque famille de matière a des caractéristiques techniques spécifiques. A partir d’une matière standard, il est également possible de faire sa propre recette en ajoutant des adjuvants pour améliorer les caractéristiques (fibre de verre,agent ignifugeant, stabilisant UV, amélioration du choc …)
Parmi ces thermoplastiques, on trouve :
- Acrylique (PMMA)
- Acrylonitrile butadiène styrène (ABS)
- Polyamide (PA)
- Polycarbonate (PC)
- Polyéthylène (PE)
- Polypropylène (PP)
- Polychlorure de vinyle (PVC)
- Polyoxyméthylène (POM)
- Polyuréthane (PU)
- etc.
Les thermodurcissables, en revanche, conservent leur état solide après polymérisation. Les liaisons chimiques sont irréversibles, ils se décomposent à la chaleur et une fois refroidis, ils ne se reforment pas. Le recyclage est impossible.
Parmi les thermodurcissables, on trouve :
- Epoxy
- Polyester
- Polyuréthane
- Silicone
- Caoutchouc vulcanisé
- etc.
Les avantages du moulage par injection
Les produits de l’injection sont divers et variés, ils nous accompagnent au quotidien que ce soit au travail ou à la maison. Les produits de consommation, de jouets, dans l’automobile, le médical ou encore la plomberie…
L’un de ses principaux avantages est la rapidité de production. La machine effectue le travail très rapidement et de manière automatique. Une fois le produit refroidi, on peut passer à une autre production.
La presse peut avoir plusieurs moules permettant la production en masse et rapidement. Un moule pré-série permet d’obtenir des produits solides et de bonne qualité. Le moulage par injection permet la production de pièces extrêmement complexes (dont la forme influe le coût).
Le moulage par injection, bien que coûteux initialement, n’a pas de concurrence pour ce volume de production. Une fois l’outillage prêt et fonctionnel, les cycles durent quelques secondes. Les séries de production sont ensuite de quelques milliers de pièces plusieurs millions avec un coût unitaire moindre.
En résumé, après une industrialisation de quelques mois, l’investissement de départ est amorti sur les productions, on parle alors de vie série.